Threads are essential components in various everyday products, and understanding how they’re made involves exploring the main manufacturing methods, such as plastic-working and metal cutting. Let’s take a closer look at these methods.
Table of Contents
Plastic Working Methods
Cold Forming

Standard bolts, screws, and nuts are commonly manufactured using multi-station machines that employ cold-forming techniques. The raw material used in this process is a metal coil that is shaped through multiple stages to attain its final form. Once the shape has been achieved, the nuts are threaded by tapping, and the bolts are thread-rolled. (See the explanation of these threading methods below)
Thread Rolling

Thread Rolling is the predominant cold working method used for producing threads. This technique is widely used for mass production of bolts and screws. However, it is also used sometimes in machining (mainly on cam-driven screw machines)
Thread rolling is a forming process where the material is squeezed and forced through a set of dies with the ‘negative thread profile’ on them, similar to a mold for forging or casting. When the threads are formed, the dies push into the material to form the minor diameter and the root radius. More than 50% of threads produced in the industry are produced using this method.
Metal Cutting Methods
On the other hand, metal cutting utilizes various methods, including taps, dies, milling, grinding, and turning. When cutting or grinding a thread form, the starting diameter of the workpiece is the major diameter of the thread. Subsequently, the material is subtractively removed during the cutting or grinding process to achieve the final thread form. Let’s explore each one of them in more detail.
Taps
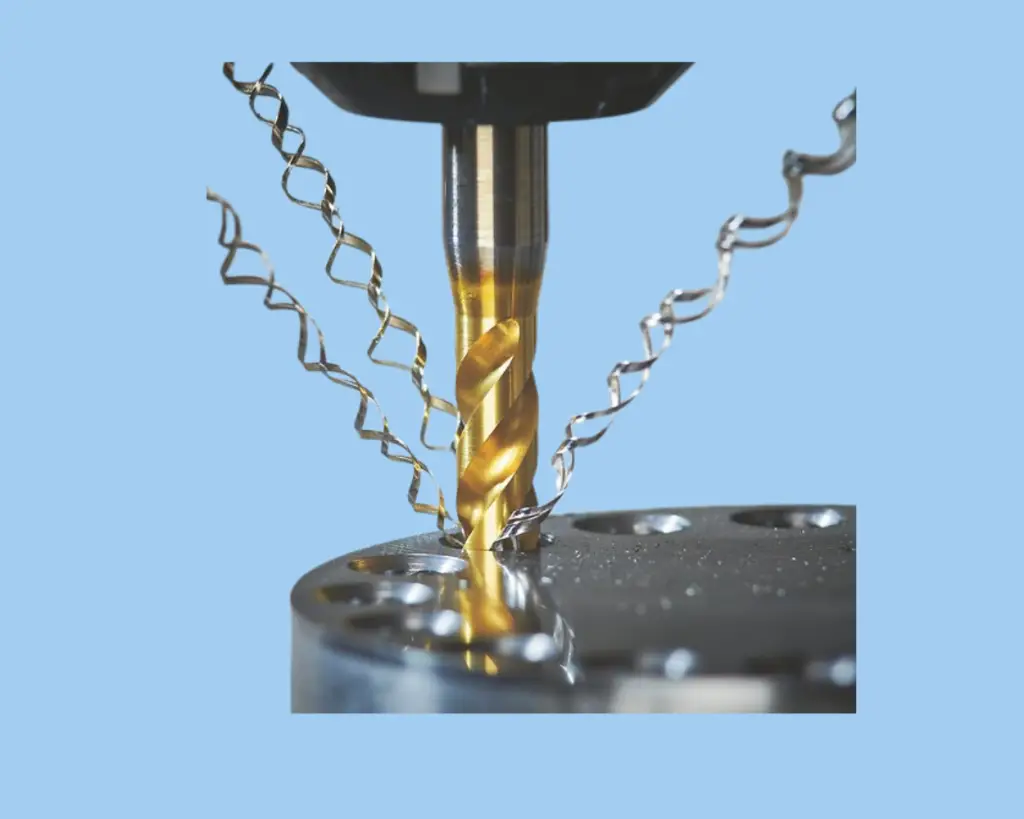
Tapping is the process of creating threads in a workpiece using a tapping tool that enters an existing hole axially. The tap size matches the hole’s dimensions. The workpiece rotates at a low speed, and the tap, fixed in a synchronized holder, supports the threading process to produce a thread.
Dies

A threading die is a tool for external threading on a workpiece. It rotates around the workpiece, cutting threads into it. The die size corresponds to the desired thread dimensions. The workpiece remains stationary, and the threading die, secured in a holder, creates threads as it rotates.
Thread Milling

Thread milling differs from tapping as it doesn’t directly link the thread geometry to the tool. The thread shape results from the rotation of the milling cutter and the simultaneous helical interpolation movement of the machine. Using a thread milling cutter allows the production of various thread diameters with the same pitch, suitable for both left and right-handed threads.
Thread Grinding

This precision machining process employs a grinding wheel to create threads on a workpiece, ensuring high accuracy and tight tolerances. This operation is typically used for threads used to manufacture taps, measuring tools, and thread gauges.
Thread Turning

A common lathe operation, thread turning utilizes a cutting tool to cut threads onto a workpiece’s outer or inner surface. The tool moves alongside the workpiece, producing the thread with specific pitches and lengths. Deeper threads may require multiple passes in which a carbide insert shaped like a thread is used for the task. Success typically depends on precise machine setup, especially when initiating the helix from the same starting point in multiple passes.

Author Bio:
With three decades of manufacturing experience, David Morr has been the ‘Global Engineering Education Expert’ at Seco Tools since 2021. Hailing from Sydney, Australia, he’s known for insightful content like “6 Essential Tool Maintenance Tips for Machinists” and “Beginner’s Guide to CNC Milling Operations and Strategies.”
Read more about David.