Índice
Generador de programas CNC de fresado de roscas en código G
Obtenga el programa CNC Gcode para su rosca en función de los siguientes parámetros:
- Controlador CNC
- Materia prima
- Geometría de la herramienta de fresado de roscas
- Manejo de la rosca (mano derecha / izquierda)
- Método de fresado (Avance / Desbaste)
- Número de pasadas
- Condiciones de corte
- Y mucho más
Para utilizar el generador de código G con eficacia y obtener resultados óptimos, es esencial tener una sólida comprensión de los términos y las teorías.
Trayectoria básica de fresado de roscas
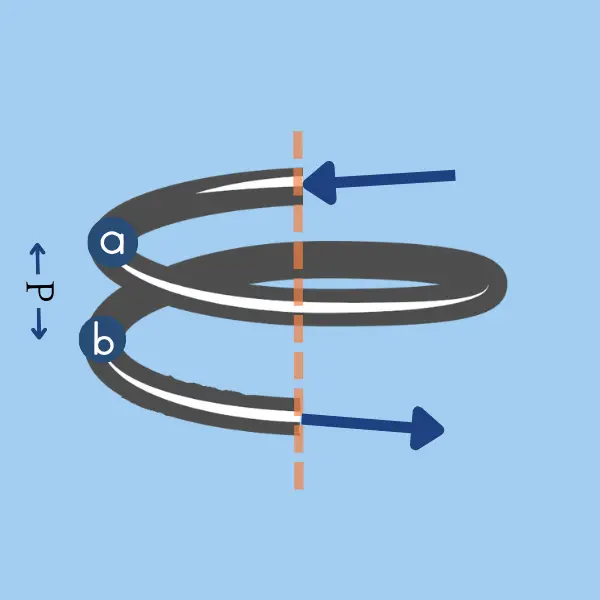
Para realizar una operación de fresado de roscas es necesario un movimiento en espiral. La interpolación helicoidal es una trayectoria de herramienta CNC a lo largo de una trayectoria helicoidal. Este movimiento en espiral combina un movimiento circular (G02 o G03) en el plano XY con un movimiento lineal simultáneo en la dirección Z.
La distancia Z del punto A al B es igual al paso (O el avance en roscas de varios pasos).
El diámetro mecanizado por la punta de la herramienta de corte es el diámetro mayor de la rosca en roscas interiores o el diámetro menor de la rosca en roscas exteriores.
- Segmento de aproximación: La fresa se desplaza desde el exterior de la rosca hasta alcanzar toda la profundidad de la rosca en el punto A. La trayectoria de la herramienta debe ajustarse de forma que entre tangencialmente en el corte.
- Segmento de roscado: Del punto A al B, el cortador se mueve 360 ° en un movimiento circular mientras se mueve simultáneamente el paso en la dirección Z.
- Segmento de retracción: A partir del punto B, la cuchilla sale del material.
A continuación se muestra el código G para una rosca interior M10X1 cortada con una fresa de roscar de 5 mm
G03 X1.25 Y1.25 Z0.125 I0 J1.25 F251 (Approach)
G03 Z1.0 I-2.5 J0 F501 (Thread Interpolation)
G03 X-1.25 Y1.25 Z0.125 I-1.25 J0 (Retract)
Herramienta de fresado de roscas/Configuración de roscas
Existen tres configuraciones posibles para Herramienta/Rosca, cada una con sus propias ventajas e inconvenientes, que requieren una estructura de programa CNC diferente.
Un solo diente
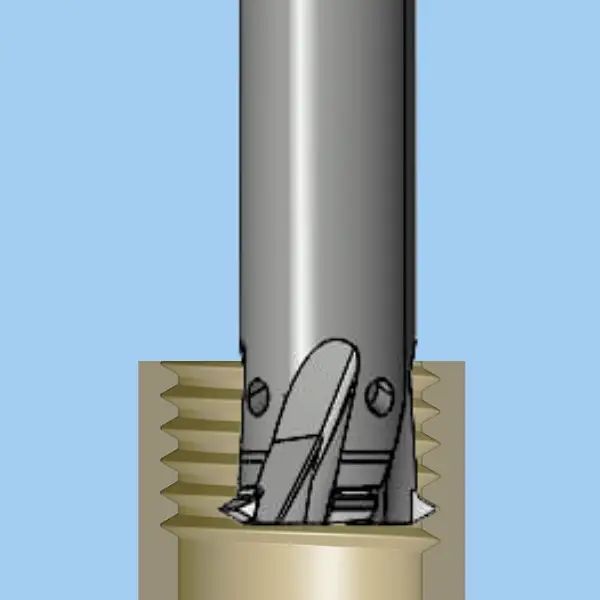
En este escenario, la herramienta realiza una trayectoria de herramienta continua, completando numerosas rotaciones completas según la longitud de la rosca dividida por el paso. Las ventajas son que se ejerce menos carga sobre la herramienta (ayuda a reducir las vibraciones) y que la herramienta es más barata. La desventaja es que esta configuración produce el tiempo de ciclo más largo.
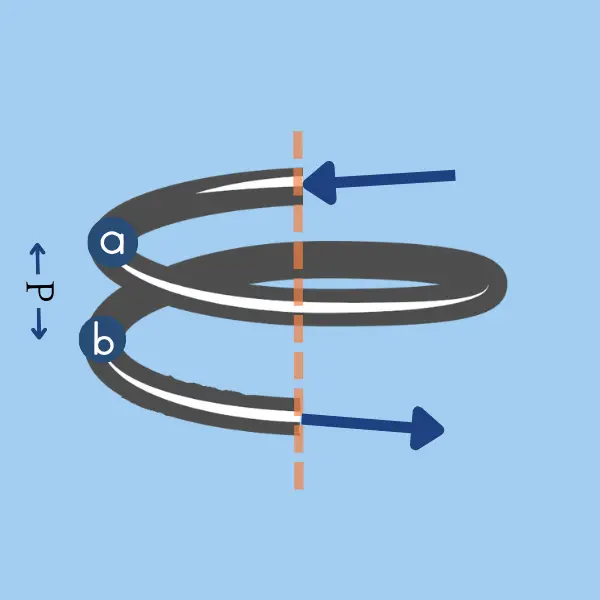
Ejemplo de código G:
G03 X1.268 Y1.268 Z0.125 I0 J1.268 F253 (Approach)
G03 Z1.0 I-2.535 J0 F505 (Single Helical Interpolation)
G03 X-1.268 Y1.268 Z0.125 I-1.268 J0 (Retract)
Dentado múltiple (longitud de la cuchilla mayor que la rosca)
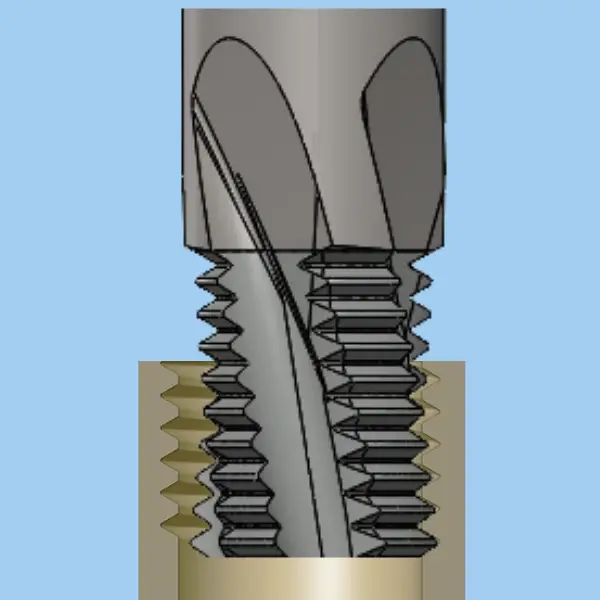
Este escenario tiene dos grandes ventajas y es la primera opción salvo cuando la carga es demasiado elevada. En primer lugar, el tiempo de ciclo es el más corto y, en segundo lugar, el programa CNC es el más sencillo. Esto se debe a que la herramienta sólo necesita realizar un único movimiento de 360° para completar la operación. Sin embargo, hay que tener en cuenta que la herramienta tiene un precio más elevado y experimenta mayores cargas.
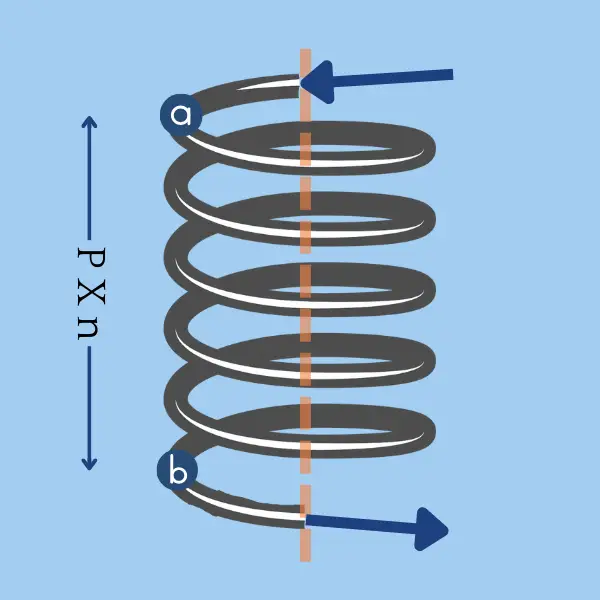
Ejemplo de código G:
G03 X1.268 Y1.268 Z0.125 I0 J1.268 F253 (Approach)
G03 Z1.0 I-2.535 J0 F505 (Helical interpolation n times)
G03 Z1.0 I-2.535 J0
G03 Z1.0 I-2.535 J0
... n times ...
G03 Z1.0 I-2.535 J0
G03 X-1.268 Y1.268 Z0.125 I-1.268 J0 (Retract)
Dentado múltiple (longitud de la cuchilla más corta que la rosca)
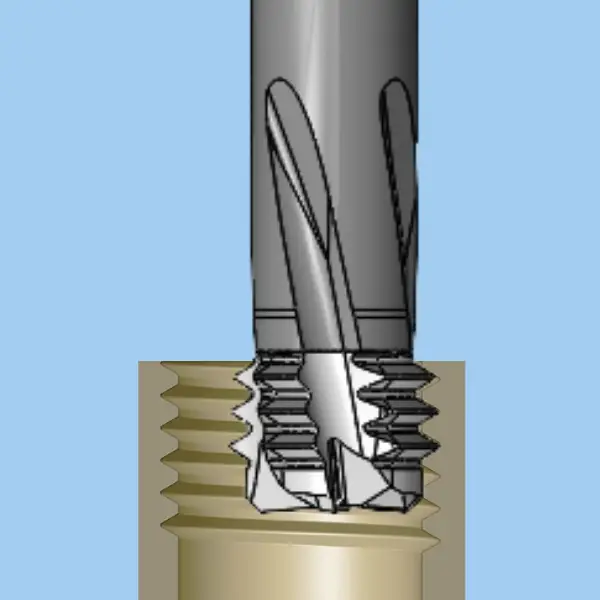
Cuando la rosca es muy larga, o la carga es muy elevada, es necesario utilizar esta configuración. Sin embargo, tiene dos desventajas principales. En primer lugar, el programa CNC se complica. En segundo lugar, puede haber un ligero desajuste entre iteraciones, ya que la operación no es continua.
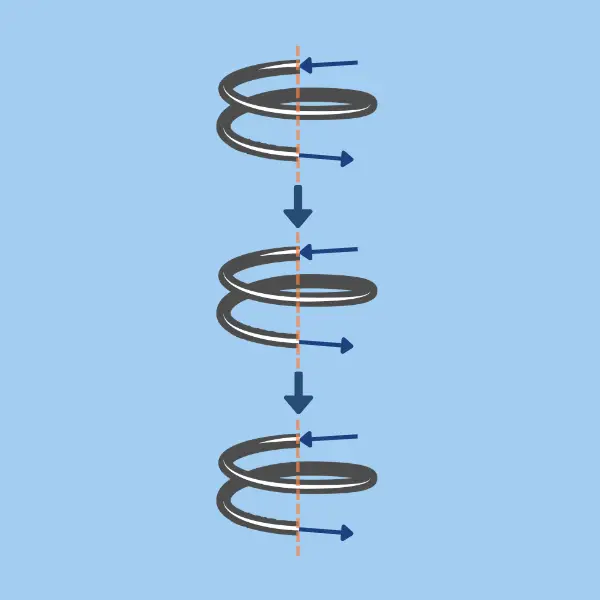
Ejemplo de código G:
(First Cycle)
G03 X1.268 Y1.268 Z0.125 I0 J1.268 F253 (Approach)
G03 Z1.0 I-2.535 J0 F505
G03 X-1.268 Y1.268 Z0.125 I-1.268 J0 (Retract)
(Skip to next segment)
G01 G40 X-1.268 Y-1.268 F2000
G01 Z3.75
(Second Cycle)
G91 G01 G41 D1 X1.268 Y-1.268 F1003
G03 X1.268 Y1.268 Z0.125 I0 J1.268 F253
G03 Z1.0 I-2.535 J0 F505
G03 X-1.268 Y1.268 Z0.125 I-1.268 J0
(Skip to next segment)
G01 G40 X-1.268 Y-1.268 F2000
G01 Z3.75
(And so on for seveal segments)
Métodos de fresado de roscas
Fresado de avance (Fresado de penetración)

En el fresado de avance, el fresado se mueve en la misma dirección que el avance. Es la primera opción en la mayoría de los casos de fresado de roscas. Al utilizar este método, el grosor de la viruta comenzará en el máximo y disminuirá gradualmente. Esto significa que el calor generado se transferirá a la viruta en lugar de a la fresa. Como resultado, el desgaste será más lento y la vida útil de la herramienta aumentará. Las virutas se eliminarán detrás de la fresa, lo que reduce la posibilidad de volver a cortar, lo que proporciona un mejor acabado superficial.
Fresado convencional (Fresado de avance contrario)

En el fresado convencional, la fresa gira en sentido contrario al de avance. A medida que el diente de la cuchilla penetra en el material, el espesor de la viruta comienza en cero y aumenta gradualmente hasta alcanzar su tamaño máximo cuando el filo de corte sale del material. Esta técnica genera calor en la zona de corte y somete a la fresa a una fuerte carga repentina durante el contacto inicial con la pieza. El resultado es un desgaste más rápido y una menor vida útil de la herramienta. Además, las virutas son arrastradas hacia arriba por el diente y caen delante de la fresa, dañando el acabado superficial.
¿Cuándo elegir el fresado convencional frente al avance?
En la mayoría de los casos, el fresado por escalonamiento es la primera opción para el mecanizado de roscas debido a la menor carga que soporta la fresa, la mayor duración de la herramienta y el mejor acabado superficial. Sin embargo, hay casos en los que es preferible el fresado convencional.
- Si la máquina no compensa la holgura, la dirección de la fuerza de corte en el fresado convencional cierra la holgura.
- Al mecanizar hierro fundido o materiales endurecidos, porque el corte comienza por debajo de la superficie del material.
Instrucciones de fresado de roscas
La dirección de 3 movimientos dicta la estructura del programa CNC:
- La cuchilla gira siempre en el sentido de las agujas del reloj (M3).
- El movimiento helicoidal de la cuchilla puede ser en sentido horario o antihorario. (G02 o G03)
- El movimiento en la dirección Z puede ser desde la parte superior de la rosca hacia abajo o desde la parte inferior hacia arriba.
Las direcciones requeridas dependen de 3 factores:
- La mano: Mano derecha o mano izquierda.
- Tipo de rosca: ¿Externa o interna?
- Método de fresado: ¿Avance o convencional?
Milling Method | Climb | Conventional | ||
Thread Handness | Right | Left | Right | Left |
Internal |
![]() |
![]() |
![]() |
![]() |
External |
![]() |
![]() |
![]() |
![]() |
Introducción del material (Trayectoria de aproximación)
Cuando una fresa de roscar penetra en la pieza de trabajo en línea recta perpendicular a la pieza de trabajo, puede provocar la rotura de la fresa o una marca en la pieza de trabajo. Para evitar este problema, se recomienda aproximarse a la pieza con un avance lento a lo largo de una trayectoria de herramienta que penetrará en el material tangencialmente. Este método permite que la carga aumente gradualmente, lo que resulta en un punto de entrada más suave con menos riesgo de marca en la pieza. La misma metodología debe aplicarse en la trayectoria de retracción al salir de la pieza (excepto para el avance, que puede ser más rápido).
Fresado de roscas interiores

- Movimiento rectilíneo rápido desde el centro a lo largo de la línea de 45° hasta una distancia de seguridad de la pieza.
- Movimiento lento y arqueado que penetra tangencialmente en la pieza.
- El avance de entrada suele ajustarse al 50% del avance utilizado en el mecanizado de la rosca.
Fresado de roscas exteriores

- Movimiento rectilíneo rápido desde el centro a lo largo de la línea de 45° hasta una distancia de seguridad de la pieza.
- Movimiento lento y arqueado que penetra tangencialmente en la pieza.
- El avance de entrada suele ajustarse al 50% del avance utilizado en el mecanizado de la rosca.
Selección del diámetro de fresa
Cuando se gira una rosca, la geometría resultante es perfecta. Sin embargo, cuando se utiliza el fresado de roscas, la naturaleza del proceso da lugar a una geometría de rosca ligeramente distorsionada. La magnitud de la distorsión depende de la relación entre el diámetro de la fresa de roscar, el paso y el diámetro de la rosca.
La fresa de menor diámetro proporcionará teóricamente el perfil de rosca más preciso, pero debe equilibrarse con la rigidez de la fresa.
Fresado de roscas internas:
- Diámetro de la cuchilla entre el 50% y el 70% del diámetro de la rosca.
- Un diámetro menor también ayuda a evacuar las virutas.
- El diámetro nunca debe ser superior al 85% del orificio pretaladrado.
Fresado de roscas exteriores:
- Un diámetro de corte del 70%-100% del diámetro de la rosca.
- Si la precisión del perfil no es un problema, puede utilizarse una fresa más grande para aumentar la productividad.
Número de pasadas radiales
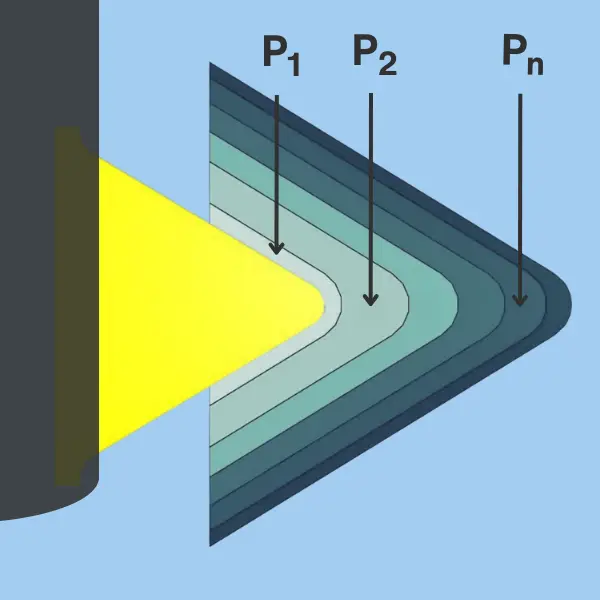
Cuando el perfil de la rosca se hace más profundo, a menudo se recomienda dividir la operación en múltiples pasadas radiales para reducir la carga sobre la fresa. Aumentar el número de pasadas puede mejorar la vida útil de la herramienta, la calidad de la superficie roscada y la estabilidad de la producción de roscas, pero da lugar a un tiempo de ciclo mucho más lento.
La elección correcta de la profundidad por pasada y del número de pasadas depende de muchos factores:
- Perfil de la rosca
- Material de la pieza
- Voladizo de la herramienta
- Número de dientes de la cuchilla
- Estabilidad
- Acabado superficial requerido
A continuación se indica el número de pasadas recomendado en función del paso y del material de la pieza. Puede utilizarlo como punto de partida y adaptarlo a su aplicación específica.
Paso [mm] | Paso [TPI] | Número de pases (*) |
---|---|---|
Hasta 1,75 | Por encima de 14,5 | 1 |
1.75 – 2.5 | 10 – 14 | 2 |
2.5 – 6 | 4 – 14 | 3 |
Por encima de 6 | Abajo 4 | 4 |
(*) La tabla muestra el número de pasadas para el acero y el acero inoxidable. Para aluminio y latón, puede utilizar una sola pasada para cualquier paso. Para el titanio y las aleaciones a base de níquel (por ejemplo, Inconel), añada 1 pasada para los valores indicados en esta tabla.
Conversión de velocidad y avance en avance de mesa
En movimientos lineales, ese avance de la mesa es Vf=Fz X Z X RPM (Donde Fz es el avance por diente y Z es el número de dientes). El avance de la mesa es el valor de avance que debe introducir en el programa CNC (o proporcionar al software CAM).
En los movimientos circulares, la fórmula es más compleja y depende de la relación entre el diámetro de la herramienta de corte y el diámetro del elemento mecanizado.
Fresado de roscas interiores
\( \large F = \frac{V_f \times \left ( \text {Diámetro de la Rosca} – \text {Diámetro de la fresa} \right )}{text {Diámetro de la rosca}} \)Fresado de roscas exteriores
\( \large F = \frac{V_f \times \left ( \text {Diámetro de la rosca} + \text {Diámetro de la fresa} \right )}{text {Diámetro de la rosca}} \)Cálculo de los diámetros mayor y menor para el programa CNC
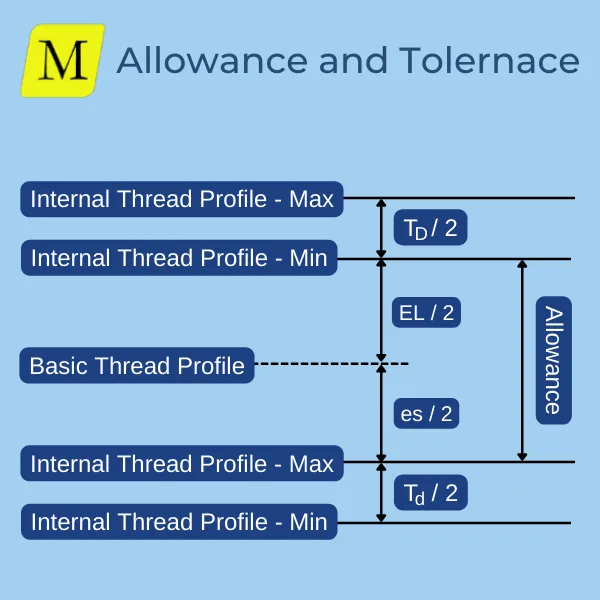
Los diámetros nominal mayor y menor de una rosca representan el «Perfil Básico» de la rosca. Sin embargo, el perfil fabricado nunca es el «básico». Es más grande en roscas internas y más pequeño en roscas externas (de lo contrario, el tornillo nunca encajará en un perno). El tamaño requerido depende de la tolerancia de la clase de tolerancia solicitada. Por lo tanto, los diámetros mayor y menor también deben desplazarse en el programa CNC. Puede utilizar nuestra calculadora de roscado para obtener las dimensiones de cualquier rosca en cualquier clase de tolerancia.
Digamos que ha adquirido los límites del perfil, ya sea a través de nuestra calculadora o por cualquier otro medio, esto es lo que debe hacer.
- Debe obtener el diámetro de paso nominal y sus límites admisibles (PD0, PDmin y PDmax) a partir de las tablas o la calculadora.
- Una vez obtenidas estas cifras, calcule la diferencia entre el diámetro de paso necesario y el básico.
Roscas Internas:
- Al crear una rosca interior, la roscadora mecaniza el diámetro mayor de la rosca.
- El diámetro mayor ajustado debe ser Dmayor + ΔPD
Roscas Externas:
- Al crear una rosca exterior, la roscadora mecaniza el diámetro menor de la rosca.
- El diámetro menor ajustado debe ser Dmenor – ΔPD
Nuestro generador de código G establece por defecto los diámetros mayor/menor ajustados para una rosca media. Puede seguir ajustando con el desplazamiento de la herramienta hasta que pase el indicador Go/No Go.