Índice
Generador de programas de código G G76
Obtenga el programa CNC Gcode para su rosca en función de los siguientes parámetros:
- Controlador CNC
- Materia prima
- Roscas y herramientas manuales (derecha / izquierda)
- Método de avance
- Número de pasadas
- Paso de acabado, chaflán, unidades, etc.
Es esencial conocer a fondo los términos que definen los ciclos de los códigos G de las roscas antes de empezar a programarlos.
Métodos de avance
Existen varios métodos para programar el modo en que la herramienta de roscado penetra en el material, cada uno con sus propias ventajas e inconvenientes, por lo que cada uno es adecuado para diferentes escenarios.
Avance radial

Es el método más sencillo disponible en todos los controladores y también puede utilizarse en un torno manual.
Casos de uso habituales:
- Pasos finos inferiores a 16 TPI (1,5 mm).
- Materiales de viruta corta como el latón y el acero de corte libre.
Ventajas:
- Puede utilizarse en un torno manual.
- Fácil de programar manualmente.
- Desgaste uniforme en ambos flancos del filo de corte.
Desventajas:
- Mal control de las virutas.
- La punta del inserto está expuesta a altas temperaturas.
- Riesgo de vibraciones debido a las elevadas fuerzas de corte.
- La profundidad por pasada es limitada, lo que se traduce en una mayor duración del ciclo.
- No es posible utilizar insertos con conformadoras de virutas.
Avance de flanco
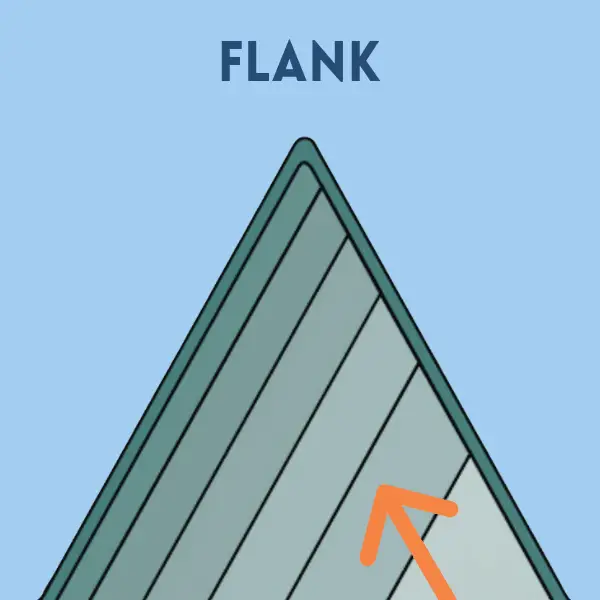
Una buena opción para todo que está disponible en todos los controladores.
Casos de uso habituales:
- Pasos gruesos superiores a 24 TPI (1 mm).
- Perfiles trapezoidales(roscas Acme)
Ventajas:
- Mejor flujo de virutas.
- Se pueden utilizar plaquitas con rompevirutas.
- Hay menos posibilidades de que se produzcan vibraciones.
- Mayor profundidad de corte por pasada, mejorando el tiempo de ciclo.
Desventajas:
- No apto para pasos finos inferiores a 24 TPI (1 mm).
- Desgaste asimétrico.
Flanco modificado

El método es el mismo que el de avance por el flanco, pero está ligeramente inclinado para evitar que el filo de la plaquita roce con la superficie del componente. No es compatible con todos los controladores. Sin embargo, si su controlador lo admite, es una opción mejor que el método de flanqueo «normal».
La aplicación consiste en restar el doble del ángulo oblicuo al ángulo del perfil. Por ejemplo, para una rosca de 60° con un ciclo de flanco modificado con 3°, debe introducir 60-2X3=56° en lugar de 60°.
Ventajas (en relación con el método del flanco normal):
- Mejor flujo de virutas.
- Menos desgaste de los flancos.
- Menor carga de corte
Desventajas (en relación con el método del flanco normal):
- No disponible en todos los controladores.(Consulte la tabla)
Flanco alterno
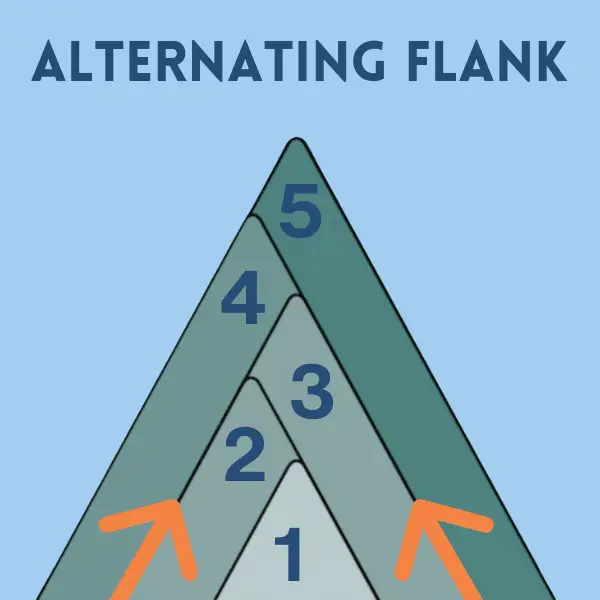
En este método, la herramienta de corte engrana con la pieza de trabajo en cada pasada desde el lado opuesto, lo que da lugar a una distribución uniforme del desgaste. No es compatible con todos los controladores.
Caso de uso común: Una mayor duración de la herramienta resulta más beneficiosa en pasos superiores a 5 TPI (5 mm) con mucho material que eliminar.
Ventajas:
- Desgaste uniforme.
- Mayor vida útil de la herramienta.
- Carga reducida (en comparación con la alimentación radial)
Desventajas:
- Controlar las virutas es difícil, ya que se dirigen en ambos sentidos.
Profundidad por pasada
El avance determina la velocidad de avance y es mucho mayor que los avances normales utilizados en las operaciones de torneado. La altura del perfil dicta la profundidad total del corte. Por lo tanto, cortar la rosca en varias pasadas es la única forma de controlar la carga de virutas. Existen dos métodos para dividir la profundidad total en varias pasadas.
Profundidad constante
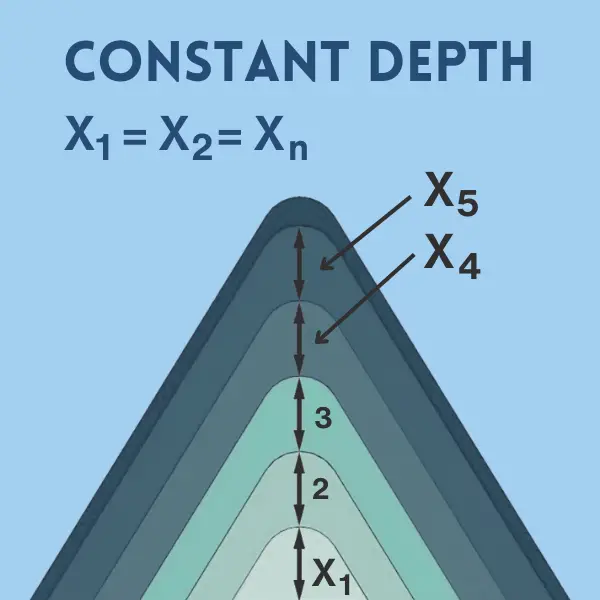
La profundidad se divide a partes iguales entre los pases. La profundidad de corte es la misma en cada pasada, por lo que la carga de viruta aumenta de una pasada a otra.
Ventajas:
- Mejor control de la viruta.
- Carga reducida en la punta del filo de corte.
Desventajas:
- Método menos productivo (requiere más pasadas)
- La carga aumenta en las últimas pasadas.
- Existe un mayor riesgo de vibraciones.
Volumen constante

La profundidad disminuye en cada pasada para mantener una carga de viruta constante.
\( ap_1 = \large \frac {\text{Profile Height} – \text{Finish Pass}} {\sqrt{\text {Number of Passes}}} \)
\( ap_n = ap_1 \times \left [\sqrt{n} – \sqrt {\left ( n -1 \right )} \right ] \)
Ventajas:
- Tiempo de ciclo más corto, ya que se requieren menos pasadas.
- Menos vibraciones.
Desventajas:
- Control problemático de la viruta en las últimas pasadas, ya que la profundidad se vuelve muy pequeña.
Determinación de la altura de la rosca (profundidad del perfil)
La profundidad del perfil (altura de la rosca) que necesita para programar un ciclo de roscado es
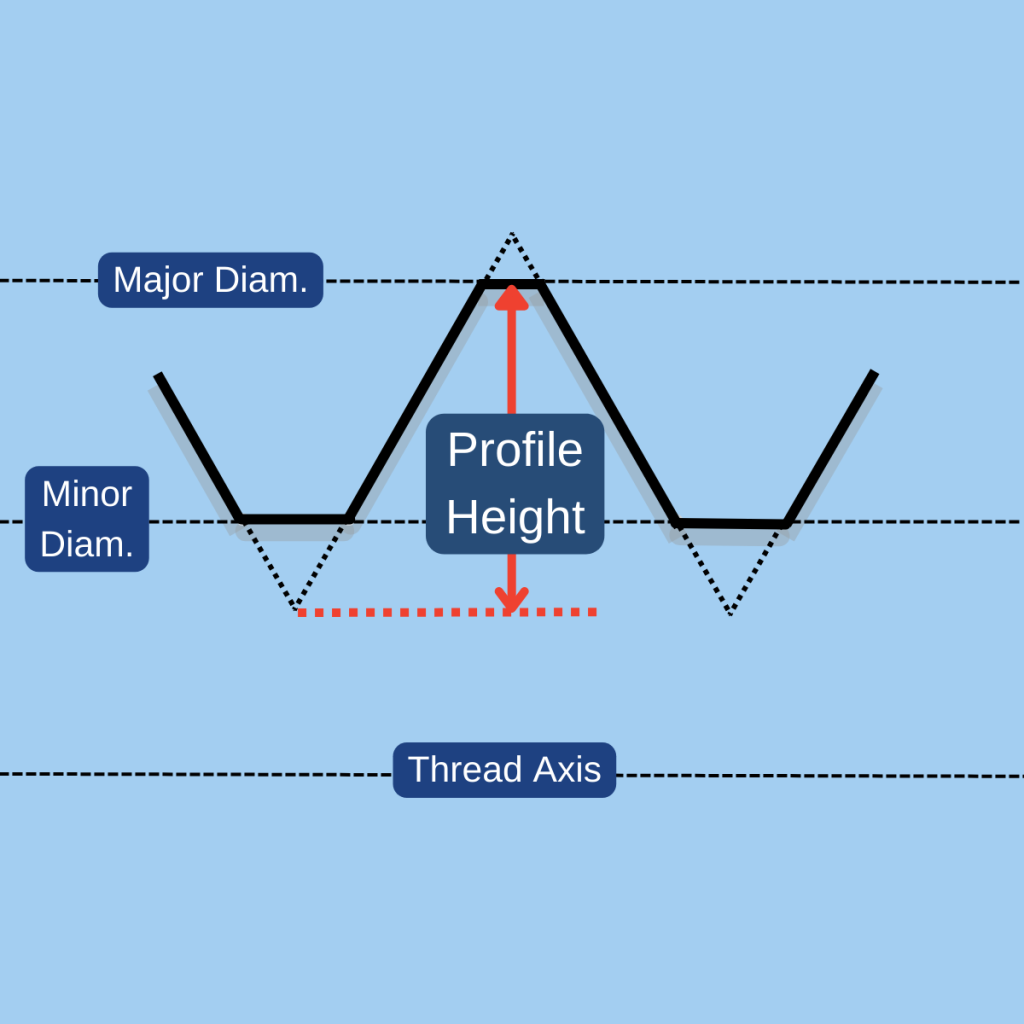
Rosca exterior:
Desde la cresta plana (o redondeada), que es el diámetro mayor, hasta el vértice teórico de la raíz. En roscas paralelas de 60 grados, como las roscas métricas estándar y las roscas en pulgada, es igual a 0,61343 * Paso.

Rosca interior:
Desde la cresta plana (o redondeada), que es el diámetro menor, hasta el vértice teórico de la raíz. En roscas paralelas de 60 grados, como las roscas métricas estándar y las roscas en pulgadas, es igual a 0,57364 * Paso.
Determinar la profundidad del primer corte
Los ciclos de roscado calculan internamente el número de pasadas necesarias y la profundidad de cada una para mantener un volumen o profundidad constante, en función de la profundidad de la primera pasada. Hay dos enfoques para decidir su valor. (El número de pasadas no es un parámetro introducido en ninguno de los ciclos de roscado).
Opción 1:
Decida cuál es la mayor profundidad que cree que puede soportar su cuchilla. El controlador decidirá el número de pasadas para mantener la misma carga de viruta que en la primera pasada (Se reducirá la profundidad en cada pasada). Con este método no es necesario hacer cálculos.
Opción 2:
Decida cuántas pasadas desea y calcule la profundidad de la primera pasada según las fórmulas siguientes:
Para el método de volumen constante
Para el método de profundidad constante
Parámetros adicionales
Algunos controladores proporcionan parámetros adicionales para personalizar el ciclo.
- Añadir un chaflán al final de la rosca (No soportado por todos los controladores)
- Añada una pasada de acabado adicional después de la secuencia de pasadas de profundidad/volumen constante. (Nocompatible con todos los controladores)
¿Qué opciones admite su controlador?
Controlador | Flanco modificado | Flanco alterno | Pase de meta | Chaflán |
---|---|---|---|---|
Okuma | V | V | V | V |
Fanuc (Formato de una línea) | X | V | X | X |
Haas | V | V | X | V |
Fanuc (Formato de dos líneas) | X | X | V | V |
Mazak | V | X | V | V |
Mitsubishi | V | X | V | V |
* Las opciones que no aparecen en el cuadro anterior están disponibles en todos los controladores.
Ahora que sabemos cómo determinar los parámetros, es el momento de ver la sintaxis Gcode para los ciclos de roscado comunes
Ciclo de roscado Fanuc G76 (formato de dos líneas)
Este formato es aplicable para:
- Fanuc tipos A, B y C. (En el tipo C, sustituir G76 por G78)
- Mazak
- Mitsubishi
G76 P__ Q__ R__
G76 X__ Z__ R__ P__ Q__ F__ (P__)
Línea 1:
P = Un código de seis dígitos en tres pares:
Dígitos 1 y 2 – número de cortes de acabado (01-99). Normalmente 00 o 01.
Dígitos 3 y 4 – Tamaño del chaflán expresado en porcentaje del plomo. 00 significa sin chaflán.
Dígitos 5 y 6 – Ángulo V de la rosca (00, 29, 30, 55, 60, 80 grados solamente). 00 se utiliza para el avance radial.
Q = La profundidad de corte mínima permitida expresada en micras. Si, según los cálculos, se necesitan profundidades menores, se ignorarán. Este parámetro se utiliza para restringir los pases innecesarios con profundidades ridículamente pequeñas.
R = La profundidad de la pasada de acabado adicional. (0,0 si no hay)
Línea 2:
X = El diámetro de la última pasada. (Diámetro menor en roscas exteriores / y diámetro mayor en roscas interiores). Debe utilizar los diámetros tal y como se explican aquí y no los diámetros mayor/menor utilizados para las mediciones.
Z = Extremo de la rosca a lo largo del eje axial.
R = La cantidad de conicidad sobre la longitud total (por lado). Se utiliza para roscas NPT y BSPT . Introduzca 0.0 para roscas paralelas.
P = Altura del perfil(véase más arriba), expresada en micras.
Q = La profundidad de la primera pasada de roscado(véase más arriba), expresada en micras.
F = el avance, que es igual al avance de la rosca (O el paso en roscas de un solo inicio).
En controladores Mazak y Mitsubishi:
* Hay un parámetro P adicional al final de la línea 2 (después de la F) que determina el método de alimentación:
P1 = Volumen constante.
P3 = Profundidad constante.
* Todos los parámeros están expresados en mm/pulgadas (No en micras)
Para ver ejemplos de Gocde con las diferentes opciones, cámbialas en el GENERADOR DE GCODE de arriba y comprueba cómo se reflejan en el programa.
Ciclo de roscado Fanuc G76 (formato de una línea)
Este formato es aplicable para:
- Fanuc serie T (T6, T11, T15, etc.)
- Haas
G76 X__ Z__ I__ K__ D__ A__ F__ P__ Q_ (M_)
X = El diámetro de la última pasada. (Diámetro menor en roscas exteriores / y diámetro mayor en roscas interiores). Debe utilizar los diámetros tal y como se explican aquí y no los diámetros mayor/menor utilizados para las mediciones.
Z = Extremo de la rosca a lo largo del eje axial.
I = la cantidad de conicidad sobre la longitud total (por lado). Se utiliza para roscas NPT y BSPT . Introduzca 0 para roscas paralelas.
K = Altura del perfil(véase más arriba), expresada en micras.
D = La profundidad de la primera pasada de roscado(véase más arriba), expresada en micras.
A = Ángulo V de la rosca (sólo 00, 29, 30, 55, 60, 80 grados). 00 se utiliza para el avance radial.
F = El avance, que es igual al avance de la rosca (O el paso en roscas de un solo inicio).
P – Ajuste del método de alimentación:
P1 = Avance por flanco o flanco modificado con volumen constante
P2 = Avance por flancos alternos con volumen constante.
P3 = Avance por el flanco/modificado con profundidad constante
P4 = Avance por flancos alternos con profundidad constante.
Q = Ángulo de desplazamiento de la rotación del husillo. El intervalo de datos va de 0 a +/-360000 (360 grados = 360000, sin punto decimal) Esta función se utiliza para cortar roscas de varias roscas. En el caso de un rosca de 3 entradas, el ángulo de desplazamiento entre cada rosca es de 120 grados. Esto significa que para cortar la primera rosca conductora, utilizamos Q=0. Para cortar el segundo y el tercer hilo conductor, utilizamos Q=120000 y Q=240000, respectivamente. Es importante tener en cuenta que la posición de inicio del eje Z sigue siendo la misma para cada rosca.
Parámetros adicionales para controladores Haas
M – Biselado.
M23 = Con chaflán
M24 = Sin chaflán
* En los controladores Haas, todos los valores se introducen en mm/Icnhes (¡No en micras!)
Para ver ejemplos de Gocde con las diferentes opciones, cámbialas en el GENERADOR DE GCODE de arriba y comprueba cómo se reflejan en el programa.
Ciclo de roscado Okuma G71
Los controladores Okuma utilizan un ciclo diferente (G71), que incluye todas las opciones mencionadas y otras adicionales. Se trata del ciclo de roscas más completo que existe.
G71 X__ Z__ A__ (I__) B__ D__ U__ H__ L__ E__ F__ J__ M__ Q__
X = El diámetro de la última pasada. (Diámetro menor en roscas exteriores / y diámetro mayor en roscas interiores). Debe utilizar los diámetros tal y como se explican aquí y no los diámetros mayor/menor utilizados para las mediciones.
Z = Extremo de la rosca a lo largo del eje axial.
A = Ángulo de conicidad. (Para roscas BSP/NPT)
I = Diferencia de radio entre el punto inicial y el punto final (expresada en radios).
* Puede utilizar un modo A o I (No ambos).
B = ángulo V de la rosca (por ejemplo, 60, 55, 29)
D = La profundidad de la primera pasada de roscado(véase más arriba), expresada en diámetro.
U = La profundidad de la pasada de acabado adicional (0,0 si no hay ninguna), expresada en diámetro.
H = Altura del perfil(véase más arriba), expresada en diámetro.
L = Distancia de biselado en el ciclo final de corte de rosca(Efectivo en modo M23; si no se designa ninguna palabra L en el modo M23, se asume que L es la distancia equivalente a un avance).
E = Tasa de variación por hilo para hilo variable
F = El avance, que es igual al avance de la rosca (O el paso en roscas de un solo inicio).
J = Número de roscas dentro de una distancia especificada por la palabra F (Cuando no se designa ninguna palabra J, el control asume J=1)
Q = Número de roscas para el roscado múltiple.
M – Patrón de corte de la rosca y modo de avance. (Se permiten hasta 3 códigos M – Uno de cada juego)
Conjunto 1
M74 = Profundidad constante
M75 = Volumen constante
Conjunto 2
M32 = Entrada de flanco (flanco derecho)
M33 = Avance por flancos alternos
M34 = Entrada de flanco (flanco izquierdo)
Conjunto 3
M22 = Sin chaflán
M23 = Con chaflán
Para ver ejemplos de Gocde con las diferentes opciones, cámbialas en el GENERADOR DE GCODE de arriba y comprueba cómo se reflejan en el programa.